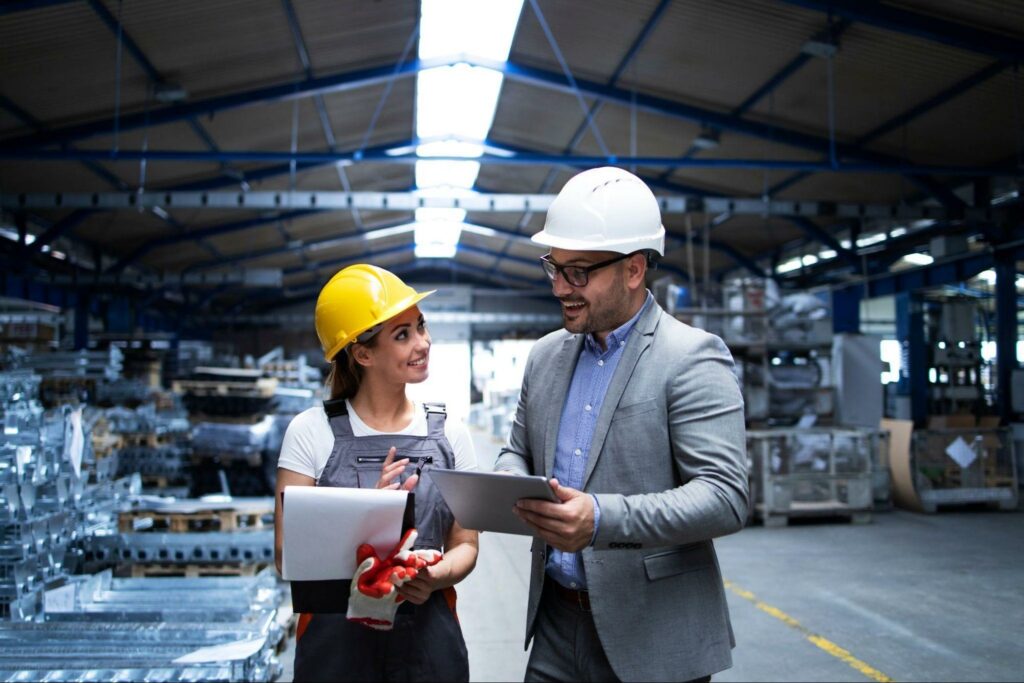
Plastic injection molding involves injecting molten plastic into a mold to create different shapes and parts. This cost-effective process is extensively used in the manufacture of plastic parts. Plastic injection molding produces an extensive range of high-quality, complicated plastic parts cost-effectively.
1. Geometry & Design Flexibility
Design flexibility is one of the main advantages of plastic injection molding. Extremely high pressure is applied to the injection molds, which forces the plastic into the mold. Injection molding can create complex and intricate designs that are usually too difficult and expensive to produce using other methods.
2. Faster Production & High Efficiency
Computer-aided design (CAD) and computer-aided manufacturing (CAM) methods create the injection mold. The designs are made to the customer’s specifications, and the mold is used to make the parts. The plastic injection molding technique is fast and allows many pieces to be produced from a single mold.
Plastic injection molding is efficient, cost-effective, and has a high production output. The speed varies depending on the intricacy and size of the mold, but each cycle takes roughly 15-120 seconds.
3. Enhanced Strength & Perfect Finishing
Fillers are used in materials and can change the plastic’s physical and mechanical prperties, increasing the item’s strength.
There are tens of thousands of injection molding materials, including high-performance blends and hybrid materials.
Most injection-molded products have a smooth surface finish close to the desired final appearance. Injection molding allows for surface treatments that don’t require further procedures, such as engraving, matte finishes, and distinctive textures
4. Flexibility to Change Color & Material
Various color and material choices are diverse, and various color procedures are available. Colors can be matched to a variety of sources such as mating parts, PMC color book, and even everyday items.
5. Reduced Waste & Lower Labor Costs
Plastic injection molding produces little waste and is environmentally friendly. The exact quantity of plastic required for a product is pressed into a mold, making it a low-waste procedure. Product design and manufacturing processes can assist in reducing waste by recycling and planning production runs to maximize efficiency and conserve energy.
Machines and robotics execute most of the injection molding process, which one person controls. Automation reduces production costs by lowering labor costs and overhead, which reduces the cost of producing parts.
6. Multiple Plastic Types can be Used at the Same Time
Injection molding can produce simple and complex items, and some techniques alter mold designs. A single mold can be used for a variety of parts or products. Complex part designs frequently necessitate the use of components comprised of several materials.
Multi-shot injection molding, or twin-shot injection molding, is a method that involves injecting two or more colors and materials into a mold. Thermoplastics, thermosets, and liquid silicone rubber are popular materials utilized in this method. The materials must have the same adhesive grade to guarantee the finished components are securely attached.
Find the Best Plastic Manufacturing Company
Injection molding has a broad range of applications and quickly generates large quantities of components. A professional plastic molding company can take your concept and make it a reality.
Universal Plastic Mold (UPM) is the best plastic injection molding near me in California. We produce accurate, durable, cost-effective plastic manufacturing services in California.